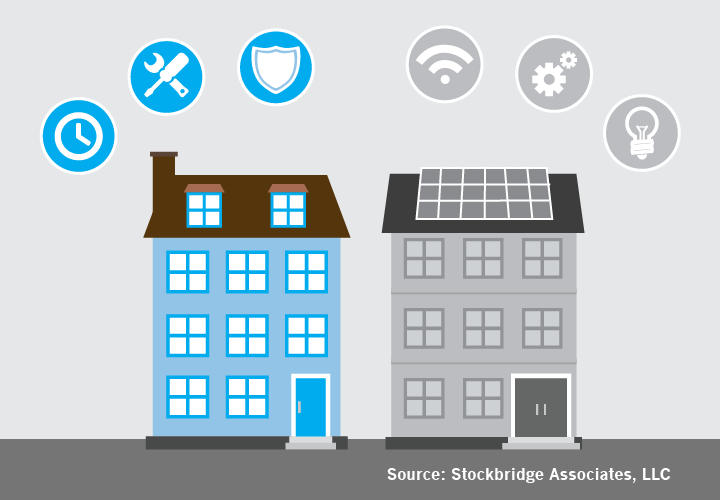
The new innovation imperative restocks working for one of the construction trades with a career full of value.
It is the end of June as I write, and I am on my annual pilgrimage to the woods of northern Maine to take my 95-year-old father in law up fishing at West Branch Pond Camps for the weekend. He has been fishing at this same place for 46 years straight and we had to keep the string running.
The camps were built in the 1880s and are constructed of local logs and branches that still seem to hold up 130 years later. West Branch Pond Camps are off the grid, too. They are about 10 miles in on a dirt road from “the tar”. No internet and no cell phone service, either. The electricity is from sundown (a little after 8 pm) until 10:00 pm and is via generator. It seems to work. Cooking is on an old wood stove in the kitchen. The food is simple and tastes great. Three squares a day.
Looking at how the cabins are framed, there is not a whole lot of difference than the logic of framing today. Not a lot of innovation, other than today we would be using milled lumber or some kind of glue-lam composite rather than tree trunks and branches.
The lack of a building code when they were built does not seem to have impaired the longevity of the structures, either. The local people who built the cabins were woodsmen and farmers who had learned the craft of putting buildings together from each other and their forefathers. It was part of the skillset one had to have in the north woods to survive.
The innovations of the current time (internet, telephone, cell phone service, 24/7 electricity) seem not to be missed, at least for a couple of days or a week.
A couple of weeks ago, I was at the Housing Innovation Alliance Summit in Chicago.
A collaboration of home builders, building product manufacturers, architects, designers, developers and suppliers of services to the industry, the Alliance is all about how home building, writ large, is evolving and will be done in the future. It was several days of collaboration and sharing of what has worked and what hasn’t worked in the continuing evolution of the industry.
We saw how advances in BIM (Building Information Modeling) are changing the ways that homes are designed and constructed. We saw how industrial designers are thinking about buildings and building systems in new ways. We got a deep glimpse into the world of the internet of things in a home and the wonders that this technology forebear.
We also learned how one solution can create another problem. As we have created homes that are highly tight and energy efficient, we have created a new problem in airflow in the home; mainly that there isn’t enough of it and the velocities are very low. The potential health effects now are a consideration and new and different air feed and return systems are required to compensate. I am not sure whether the savings in energy might be eaten up in the additional sophistication of the delivery systems needed. But that is a discussion for another day.
We also learned about new business models for home builders. New single family for-rent business models were compared to the economics of doing just for-sale, for example. The "montage” building model of Unity Homes in New Hampshire (more than panelized, less than modular) was reviewed in detail, as it enabled productivity improvements while still doing fundamental on-site construction.
We also did a deep dive into 3D printed home technology. Very cool stuff, but still in its infancy.
Despite all of the neat stuff we saw and discussed over two-plus days we were there, the discussions with builders around the tables continued to gravitate back to a more fundamental issue: the growing lack of trade labor that it takes to build homes and communities at a level that is needed to house people in the USA. Whether it is affordable housing, workforce housing, rental housing, multifamily housing, modular housing, or manufactured housing, the supply of tradespeople, both skilled and unskilled, needed to produce at the level required is just not there.
No app for the iPhone or Android is on the horizon to physically build the structures we need. We still need people with the skills and passion to be carpenters, concrete masons, electricians, plumbers, mechanical system installers, drywallers, painters, siders, roofers, glazers, insulators, and all of the other skills needed to build.
It seems to me that the real innovation needed right now is how to recreate a narrative and a system that enables and supplies sufficient trained labor to build the housing that the country needs.
Historically, the construction trades have been the first rung on the ladder of economic viability for immigrants into the country. Several generations ago, my ancestors came from Ireland and became horsehair plasterers in Boston. It was hard work and the living was hard, too. But it provided the stepping stone for subsequent generations to become cops and firemen and then their offspring had the opportunity to go to college and become builders, developers, attorneys, financiers, and other vocations.
For others born here, here, there was no real social stigma for not going on to college. In high school, there was a track for developing basic trade skills from typing, cooking and sewing to carpentry, basic electrical, basic metalwork, and basic mechanical skills. Upon high school graduation, while some went off to college, others went to work with their hands and minds in other ways.
At a high school reunion several years ago, when many of my small (84) class were near the ends of their careers, it was interesting to look at what each had done professionally.
Some who had gone on to college immediately had done well professionally, had started or were running companies, and were leaders in their respective fields. Others had not done so well and had led more modest (and sometimes scandalous) existences.
Others who had not gone on to college had a similar spread of experiences. One fellow ended up buying a second hand septic pump truck (aka a “honey wagon”) and had built a large company doing that work and then expanded to doing real estate development. He had become a pillar of the community in the process. Others had worked as mechanics and ended up owning their own garage; had become electricians and helped develop and train many other electricians; and had raised themselves up from being carpenter helpers to running homebuilding companies.
As Angela Duckworth in her bestseller “Grit” has made us all aware, the “grit’ one has is probably more important than the actual intelligence one possesses for overall success.
Yet, over the past several decades, we have seen a growing animosity toward immigrants into the US. The historic source of the bottom-rung labor for construction that eventually evolves into the skilled labor and the owners of trade contractors for that labor has dried up despite the fact that we are essentially at a point where anyone who truly wants to work has the opportunity to do so.
Even more worrying is the demonization of manual and skilled labor on an institutional basis.
The narrative that “in order to get ahead and attain a middle-class lifestyle, you HAVE to go to college” has become accepted gospel. High schools are ranked on the SAT scores they attain and the percentage of students going on to four-year colleges and the principal’s careers is determined by how well they deliver on those metrics.
The fact that only a modest percentage of those going on to four year colleges ever graduate seems to be lost in the shuffle. The latest available data shows that just 19% of students entering public colleges and universities graduate in 4 years. It jumps to 59% if the bar is set at 6 years for public universities. It increased to 65% as the 6-year graduation rate at private colleges and decreases to 32% for private for-profit colleges.
So the data implies that maybe two out of three entering college graduate in 6 years. Not exactly a slam dunk.
Even more, the economic value of a degree in engineering compared to a degree in, say, American Studies is never brought into the discussion for those who do graduate. Yet, from the same college, the cost of that diploma is about the same while the economic futures are statistically much different.
On the other hand, the track for learning key trade skills has withered in many communities for a variety of reasons. Even at the community college level, interest in construction skill tracks often wanes, despite the growing need in the industry.
It seems that going into the construction trades is not “cool.” Yet, seasoned electricians, plumbers, mechanical, and masonry trades can earn incomes in the high 5 and low-6 digit range and even more if they own their own company. These are incomes that are often equal to or higher than many four-year college graduates, particularly as the supply of these trades is now less than the demand for them.
Yet, this story of the economic viability of “the other path” has not been told well. It seems that the institutionalization of the narrative that going to college is the only path to good earnings has not been fully told in all of its nuance to the detriment of affordable housing for the nation.
So the innovation needed in the industry at this time is less about the cool software, energy improvement, and “internet of things” opportunities that are out there on the horizon. Instead, innovation is more about how a truer story of the needs and opportunities for those in the construction trades and how those can be translated into lifestyles and incomes that are worthy, also.
If this piece of innovation is not accomplished, we, as a nation, will continue to suffer a diminished lifestyle and opportunity for advancement.
This truly is an imperative.
About George Casey
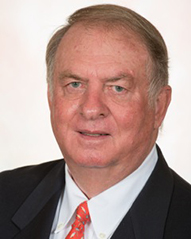
With decades of deep hands-on experience in operations and processes, business consultant and keynote speaker George Casey brings unparalleled insight to a variety of businesses to streamline operations, increase profits and long-term sustainability, especially to the residential development and home building industries.
Join Our Discussion